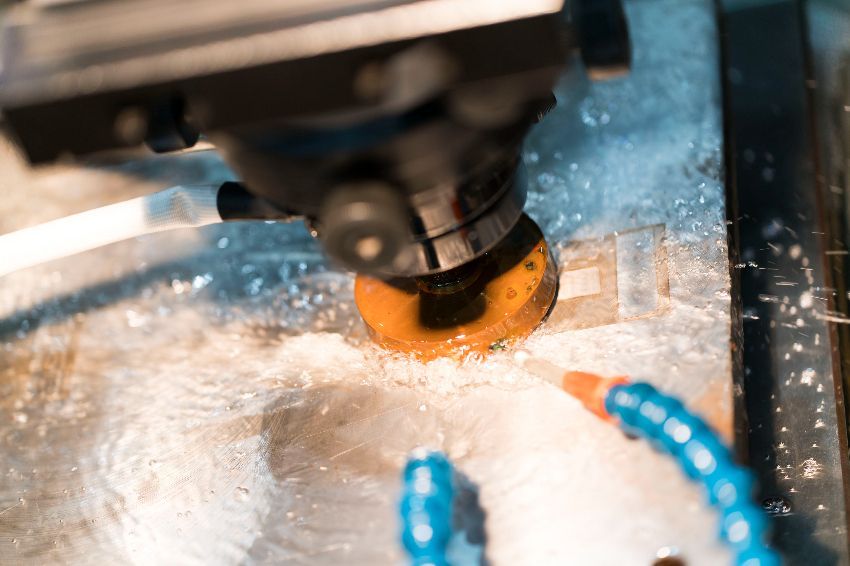
Glass / Ceramics
Grinding Glass and Ceramic:Prevents sludge solidification, no more hard sludge and clogging
Why Do Glass and Ceramics Require Specialized Cutting Fluids?
Glass and ceramics are hard and brittle materials that are highly prone to cracking and edge chipping under pressure during machining. The process also generates large amounts of fine dust and abrasive particles. Using the wrong cutting or grinding fluid can lead to surface scratches, tool damage, and coolant tank clogging. Therefore, selecting a cutting fluid with rapid sedimentation, excellent lubricity, and high fluid stability is essential.
Advantages of Fully Synthetic Cutting Fluids
Fully synthetic cutting fluids contain no mineral oil, offering excellent stability, no sticky residue, and clean, eco-friendly performance. They are especially suitable for high-precision materials like glass and ceramics. These fluids reduce spark generation, noise, and unpleasant odors during machining, while also extending coolant life and machine uptime.
Application Challenges & Differences
Unique Demands in Glass Machining
Glass machining is commonly used in optical lenses, camera modules, display panels, and high-precision instrumentation. If abrasive particles are not rapidly settled, they recirculate through the system, causing chipping, surface scratches, and accelerated tool wear. Additionally, hardened sludge buildup in the tank makes cleaning difficult and increases maintenance costs. Therefore, the key requirements for glass cutting fluids are fast settling and sludge stability.
Lubrication Challenges in Ceramic Machining
Although dry machining is common for ceramics, water-based cutting fluids are often used to manage heat and protect tool life. Materials such as zirconia, silicon nitride, and IC ceramic substrates heavily rely on the lubricating performance of the fluid to minimize noise, sparks, and inconsistent machining. Since fully synthetic fluids lack mineral oil, their performance depends entirely on the quality and stability of the additives, making product selection especially critical.
Recommended Cutting Fluids: MORESCO GR Series
MORESCO GR-5 – Designed for Glass Machining
GR-5 is a fully synthetic cutting fluid imported from Japan, specifically developed for optical and precision glass machining. It features ultra-low foaming, fast sedimentation, excellent cooling, and antibacterial performance. GR-5 effectively prevents surface scratches, edge chipping, and reduced tool life.
GR-5 is also ideal for machining quartz glass, a material known for its hardness and thermal stability. The fluid's rapid settling and high cooling capacity help prevent stress-induced cracks and improve machining cleanliness.
Key Features:
● High cooling performance to prevent thermal cracking and surface damage
● Ultra-low foaming to prevent splashing and visual obstruction
● Antibacterial and deodorizing to extend fluid life
● Chlorine-free fully synthetic formula, eco-friendly and easy to clean
Recommended Applications: Optical glass, quartz glass, architectural glass, display panels, precision lenses
MORESCO GR-4 – Designed for Ceramic Machining
GR-4 is a fully synthetic cutting fluid designed for machining high-hardness ceramics. It is suitable for zirconia, silicon nitride, ceramic rings, IC substrates, and more. GR-4 offers high lubricity and excellent stability, significantly reducing noise and the risk of tool cracking.
Key Features:
● Superior lubricity to minimize tool wear and machining noise
● Excellent stability in hard water, compatible with global water conditions
● Free of silicone and chlorine, reducing environmental and user risks
● Highly stable formula that resists odor and supports long-term use
Recommended Applications: Zirconia, silicon nitride, ceramic IC substrates, ceramic rings
FAQ
Q1:What’s the main difference between GR-5 and GR-4?
A:GR-5 emphasizes cooling and sedimentation, making it ideal for glass machining. GR-4 focuses on lubrication and fluid stability, specifically designed for ceramic machining.
Q2:Are fully synthetic cutting fluids always mineral oil-free?
A:Yes. The MORESCO GR Series uses a mineral oil-free formulation, offering enhanced stability and environmental performance.
Q3:Is GR-4 required for all ceramic machining?
A:If you're working with high-hardness ceramics such as zirconia or IC substrates, GR-4 is strongly recommended to ensure optimal lubrication and stable machining performance.
Q4:Can GR-5 be used for quartz glass?
A:Yes. GR-5 is suitable for machining quartz glass, thanks to its excellent thermal control and low-foam sedimentation, which are critical for high-hardness materials like quartz.
If you still have no idea that how to choose the right metalworking oils, please click Contact Us or send an email or call us. We will contact you as soon as possible.
Glass / Ceramics - Grinding Glass and Ceramic:Prevents sludge solidification, no more hard sludge and clogging | Taiwan-Based Metalworking Fluid Manufacturer & Supplier For 39 Years | HLJH
Located in Taiwan, HAI LU JYA HE CO., LTD has been an industrial lubricant manufacturer and supplier. Main products, include Glass / Ceramics, metalworking fluids, industrial lubricants, soluble cutting oils, semi-synthetic cutting oils, synthetic cutting fluids, neat cutting oils, rust preventive oils, slideway oils and hydraulic oils, which can reach 150 tons of cutting fluids per month.
HAI LU JYA HE Co., Ltd. (HLJH) have been focusing on manufacturing and marketing the industrial lubricants more than 30 years. Our fundamental belief is to make a harmful, friendly with lives, businesses, and leaving a lasting legacy for generations to come. We offer metalworking fluids (water-based cutting fluid, neat cutting oil), rust preventive oil, hydraulic oil, slideway oil, spindle oil, gear oil and so on that cover the whole industrial lubricant value chain. Our fundamental belief is to offer harmful and friendly products such as water-based cutting oils, neat cutting oil, rust preventive oil, hydraulic oil, slideway oil, spindle oil, gear oil and so on that cover the whole industrial lubricant value chain.
HLJH has been offering customers high-quality metalworking oils and fluids, both with advanced technology and 39 years of experience, HLJH ensures each customer's demands are met.