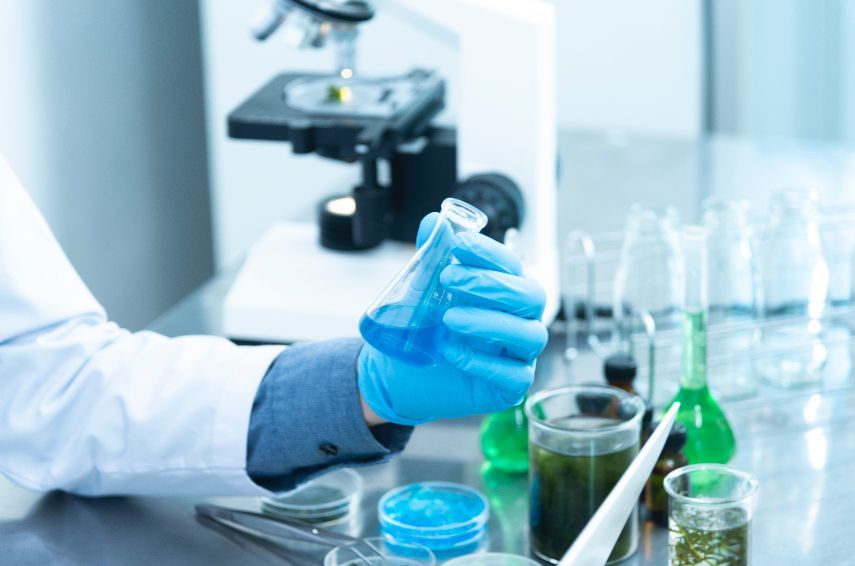
Blog
Knowledge ( Q&A )
HAI LU JYA HE Co., Ltd. (HLJH), we are a manufacturer and a supplier of industrial lubricants. We have been focusing on manufacturing and marketing the industrial lubricants more than 30 years.
Therefore, we are going to sharing our experienced and frequently questions for your reference, like「What causes FOAMING COOLANT?」「How to Select the Right Hydraulic Oil」, and so on. These articles are useful and helpful for metal processing. For sure, if you have any unclear or any questions, please feel free to contact us or email to us.
Cutting fluid, also known as coolant, plays a crucial role in machining and metalworking processes. Whether you're operating a small home workshop or managing a large industrial facility, understanding...
Read moreIndustrial lubricants (such as slideway oil, hydraulic oil and rust preventive oil, etc.) are mostly used to lessen the wear and tear of material while reducing binding and friction. And, it can prevent...
Read moreIn an era where industries are driven by precision, efficiency, and sustainability, the role of lubricants has never been more critical. Lubricants are the lifeblood of machinery, ensuring smooth operations...
Read more